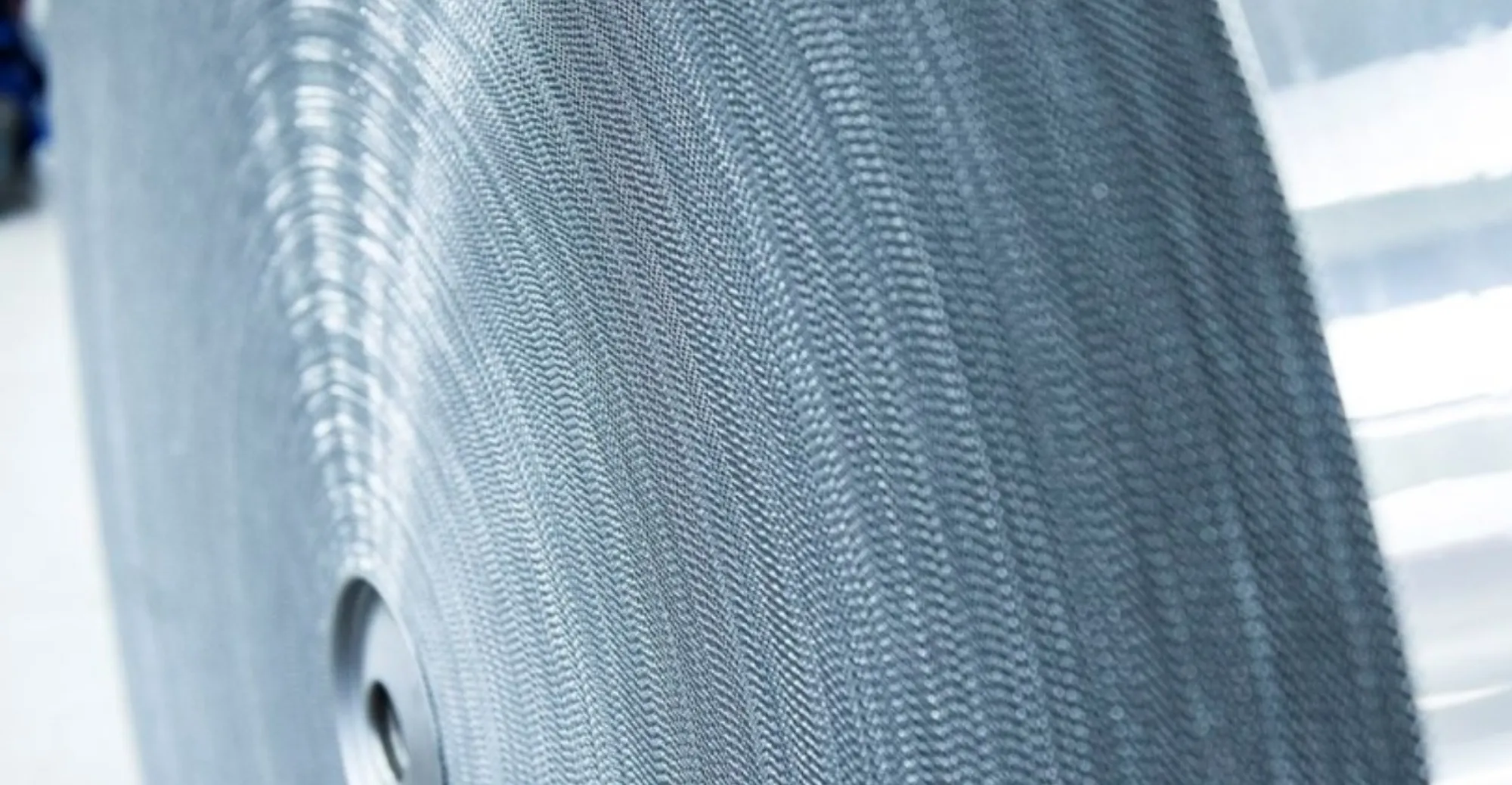
How to maintain a heat recovery wheel
How to maintain a heat recovery wheel
– by Albrand Veldhuizen, 12-02-21
Heat recovery wheels have been the subject of some controversy since the onset of Covid-19. Despite being a way to significantly save on energy, they also pose a potential threat by spreading viruses. In this blog you will learn how to maintain and operate heat recovery wheels to attain the safest results.
When the pandemic first hit us about a year ago the consensus in the world of HVAC was to turn all heat recovery wheels off. This quickly turned out to be false information and the wheels started spinning again. What caused the sudden change and what can we do to keep safe?
In this blog you will learn:
- How do heat recovery wheels work?
- What is the potential danger?
- The correct configurations.
How do heat recovery wheels work?
Let’s start with a memory refresher. In its simplicity, the heat recovery wheel is one of the most elegant ways to recover energy. A giant wheel is set at the intersection of two air streams inside the air handling unit. The wheel is made out a material with a honeycomb structure. While slowly rotating it takes the energy from the existing air and transfers this to the incoming air.
Figure 1: Principle of the heat recovery wheel
Because both air flows are separate, it does not matter whether the return air has bad smells from, for example, the toilet or a pantry. This makes it possible to recirculate the ship for 100%. All the air that comes in is fresh outside air.
Figure 2: Heat recovery wheel in air handling unit
As a result, the efficiency of the heat exchanger is increased by up to 85%. With its low resistance, the wheel is a popular heat recovery agent for large air volumes such as those found on passenger vessels.
What is the potential danger?
Although, technically speaking, both air streams are separate, the wheel itself rotates through both supply and exhaust air streams. There is a possibility of internal leaks. How about stopping the heat recovery wheel from spinning to avoid contact between the incoming and exhaust air flows?
First, this would drastically reduce the air handling unit’s energy efficiency, causing losses of up to 85%. And secondly, it doesn’t solve the problem.
The main indicator of internal leakage is expressed by the Exhaust Air Transit Ratio (EATR) in %. Yes, it is caused by the rotor speed and purge sector, but most of all by the pressure difference between the exhaust and supply section.
Figure 3: Internal leakage (source: Rehva)
It is important to keep overpressure on the supply air side. Any leak will be from supply to exhaust.
The correct adjustments
A well designed and perfectly maintained heat recovery wheel usually has an EATR below 1% and a contamination ratio that is practically without meaning. This can only be achieved if the wheel is kept in good shape during commissioning and via inspections and regular maintenance.
Figure 4: Configuration with both fans after rotor (source: Rehva)
Figure 5: Configuration with both fans upstream of the exchanger (source: Rehva)
Balancing pressure differences
Leakage can be minimised by setting up the correct pressure difference. The pressure at p11 should be at least 20 Pa lower than the pressure at p22. You can achieve this by adjusting the damper as follows:
- Adjusting the damper in the exhaust air section so p11 becomes at least 20 Pa less than p22. See figure 4 for this configuration.
- Adjust the damper in the supply air section so p11 becomes at least 20 Pa less than p22. See figure 5 for this configuration.
Conclusion
One of the most efficient means of energy recovery, heat recovery wheels have been installed in many vessels. The onset of coronavirus made us reconsider our views on ventilation and heat recovery wheels, leading to a set of measures including the ones above.
The information in this article is based on appendix 2 of the Rehva Covid-19 guidance version 4 of November 2020. Here you can find many more tips on how to maintain heat recovery wheels. Please be aware that this advice is based on the latest available scientific knowledge of the pandemic and subject to change.
Albrand Veldhuizen | Commissioning Engineer
Albrand has been working at Heinen & Hopman since 2006. He has worked himself up to the position of Commissioning Engineer and nowadays he is stationed at one of the largest yacht builders in Germany. During his many years working onboard numerous luxury yachts, he has developed a great expertise in HVAC systems for superyachts.