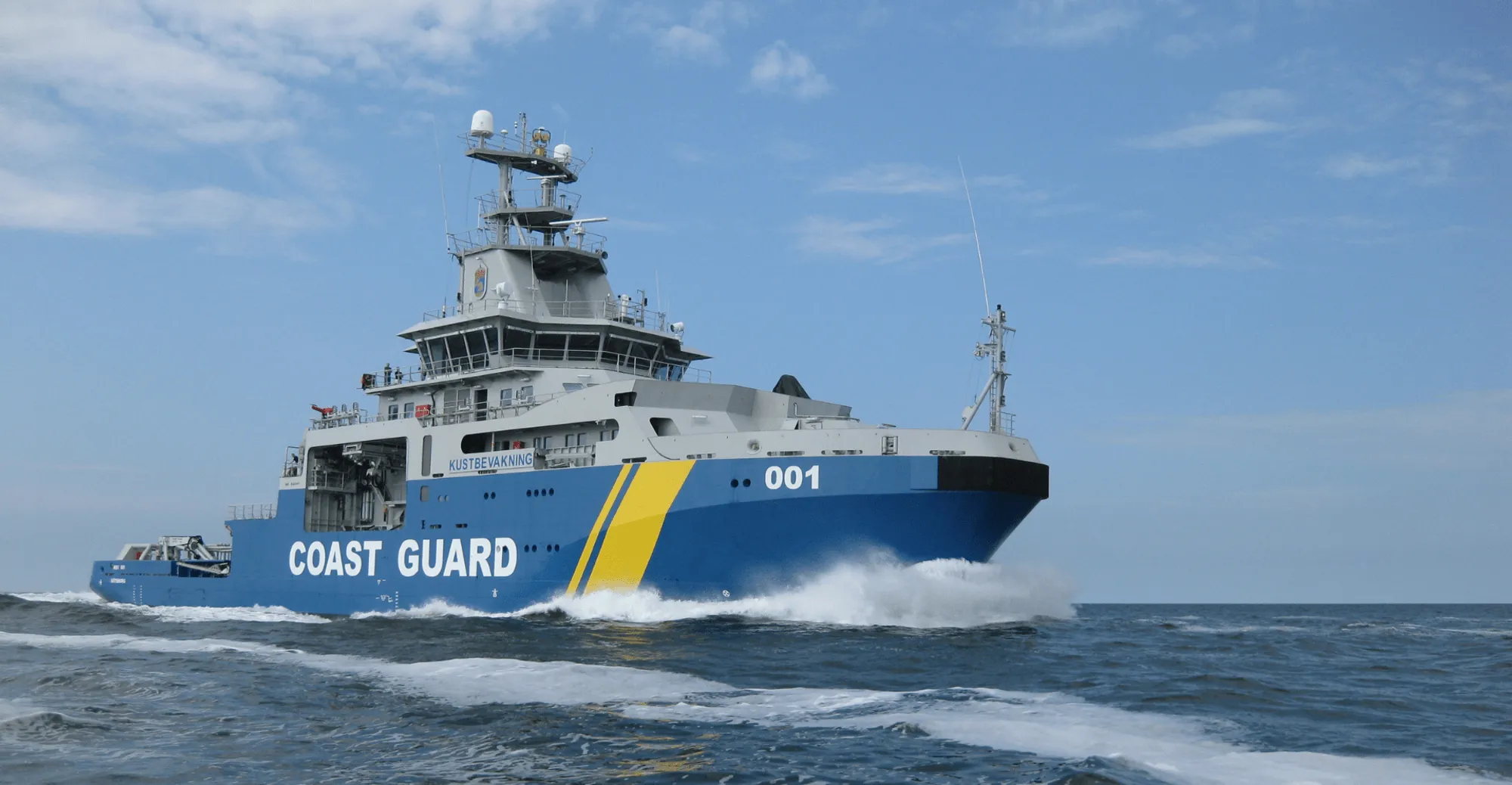
KBV 003 Amfitrite
Country of delivery | The Netherlands |
Delivery year | 2010 |
IMO NO. | 9380465 |
Length | 81.30 m |
Name vessel | KBV 003 Amfitrite |
Owner | Swedish Coastguard |
Shipyard | Damen Schelde Naval Shipbuilding |
Subsidiary | H&H Headquarters |
Vessel type | Multi Role Vessel |
HVAC | Multi Purpose Vessel
In 2006, Heinen & Hopman acquired the order for the delivery of HVAC systems onboard two identical Swedish Coastguard vessels, KBV-001 and 002. In addition to what is typically found on such vessels, the operational capability of these boats includes an oil spill recovery mode. This meant that a special air filtering system capable of eliminating hydrocarbon compounds had to be added to the interior air conditioning. Although this was not required by class, the client needed the capacity to filter these compounds in order to ensure a healthy working environment for the crew.
In 2007, KBV-003, a third boat in the range with an additional chemical recovery function, was added to the order. This created a whole new dimension to the vessel as chemical recovery conditions can be very harmful to the crew. Germanischer Lloyd (GL), the relevant classification authority, had specific requirements for crew safety, although the exact specifications on what compounds should be filtered from the air were as yet undefined and beyond any class requirements existing at the time.
Tough challenges
We had learnt from KBV-001 and 002 that the space available on the vessel was extremely limited. This was a major challenge as the Swedish Coastguard had lots of very demanding requirements regarding the level of technology applied, especially when it came to energy saving solutions, crew comfort and operating possibilities.
The following systems were custom built for these purposes:
- Air conditioning unit with enthalpy exchanger, specially designed to fit into the HVAC room. The usually rectangular box unit was divided into sections, keeping the same functionality but with a totally different appearance.
- Oil recovery carbon charged filtering systems for accommodation areas and wheelhouse.
- The HVAC controls were fully automated and connected to the vessel’s integrated monitoring system. The various operating modes (normal, silent, oil recovery, locked ship) are available at the push of a button.
- High-level vibration/ noise reduction to ensure Comfort Class 2 for the well-being of the crew.
- Various control and monitoring systems providing temperature/ pressure control in various systems. This optimised the power requirements of the equipment under all operational situations and ambient conditions.
Additional challenges for KBV-003:
- Added Chemrec mode, also available at the push of a button.
- Chemrec filtering systems for accommodation and engine room, much more elaborate than the Oilrec systems for vessels 1 and 2. This featured an additional backup system, fully automated in case the filters become saturated.
- Obtaining GL approval on the filtering systems. The requirements of the Swedish Coastguard were such that they had never been dealt with under class and had no 1:1 comparison with previously built systems. In close cooperation with the Swedish Coastguard, the yard and Dutch research institute TNO, approval tests and procedures ensured an excellent solution for the client, suitable for class approval.
Scope of work
Heinen & Hopman’s scope of work for the KBV-003 project was:
Pre-contract
Co-writing technical specifications and implementing the HVAC system into the vessel design.
Post contract
Elaborating the complete design and engineering of the HVAC and PCP system. This was followed by delivery, installation, launch, FATs, HATs, SATs and ILS activities.
The vessel was constructed by Damen Schelde Naval Shipbuilding in the Netherlands.
Scope of supply
In addition to several smaller pieces of equipment, the following main components were supplied:
- 1 Air handling unit with enthalpy exchanger accommodation – 21.400m3/hr
- 1 Air handling unit wheelhouse – 8.400m3/hr
- 10 Local cooling units – Var. cap.
- 2 Filter units for accommodation and ER room – 2+2 stage Hepa / Carbon
- 2 Backup filter units for accommodation and ER room – 2+2 stage Hepa / Carbon
- 8 Closed condition local cooling units for engine rooms – 16.000m3/hr
- 2 Local cooling units for thruster rooms – 6.000m3/hr
- 18 Fans for mechanical supply ventilation
- 1 High pressure “Dirivent” supply ventilation for ER
- 22 Fans for mechanical exhaust ventilation
- 2 Chilled water units – 180kW each
- 2 Chilled water pumps – 54m3/hr, speed controlled
- 2 Oil fired boilers – 550kW each
- 2+2 Hot water pumps primary and secondary systems – 34m3/hr + 20m3/hr
- 21 Local unit heaters
- 2 Special purpose drying units
- 2 Provision cooling plants, PLC controlled – 6,5kW (100% + 100% backup)
- 1 Fully automated HVAC control system – PLC + IAMCS interfacing
- 1 Outside Mist eliminators with heat tracing for ER
Do you want to know how our HVAC can benefit your vessel?