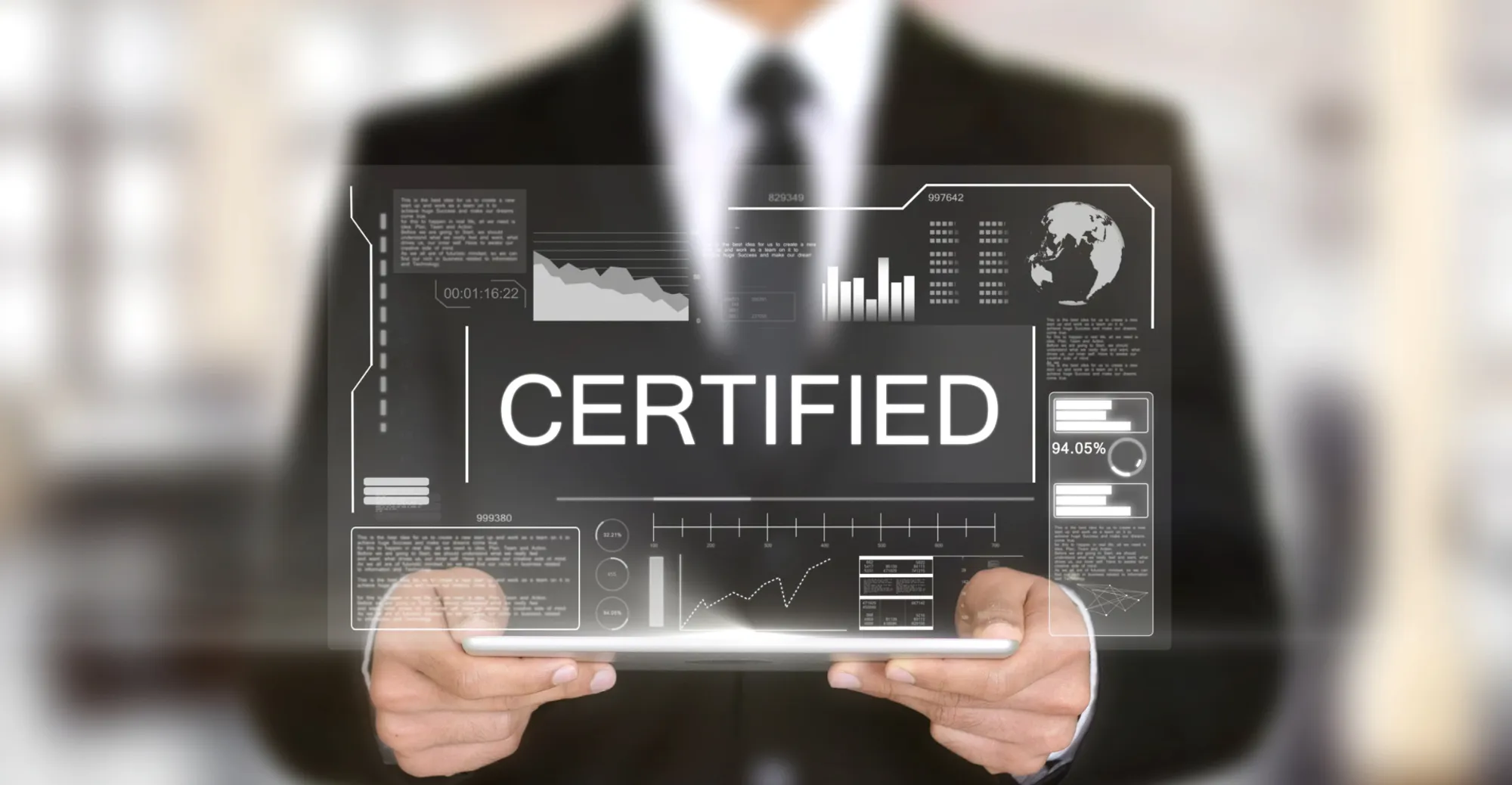
What it takes to keep certifications up to date
What it takes to keep certifications up to date
As a Quality Engineer, one important part of my job involves seeing to it that all the certifications we have for our marine heating, ventilation and air conditioning (HVAC) business are kept up to date. Most of the time this is a paper exercise; but there are some certifications that require testing, and visits to external work sites and to suppliers of our products.
The certifications we have are issued by several organisations known as notified bodies. They are authorised to issue certificates to organisations that have demonstrated compliance with legislation, and with rules and regulations issued by national authorities and industry associations, the European Union (EU), and the International Organization for Standardization (ISO), for instance.
There are legal certifications (compliance with regulatory requirements), those covering one or another aspect of the business, those related to health, safety and the environment (HSE) and quality. Some shipyards are required to ensure that certain parts of the installations we supply for ships they are building have valid certificates.
All told, there are about 35 certificates to maintain.
Certification: four why’s
There are four main reasons why keeping certifications up to date is important. Two are fairly straightforward: first, we are required to under Dutch law. Non-compliance is not an option.
The second reason is commercial: If we do not have certain certificates, such as ISO 9001, customers will simply not do business with us.
The third has to do with EU legislation. For some products that are installed on board ships built within the EU, we must have a certificate issued pursuant to the EU’s Marine Equipment Directive (MED). A product that has an MED certificate meets common standards of safety and performance, and thus helps ensure a safe environment for every passenger on the ship. Our customers are themselves required to insist that, where applicable, the products we are supplying them with bear all the required certifications. So that’s a key business reason: no certificate, no contract.
The regulatory environment when it comes to supplying products for ships in particular is super-strict: up-to-date certificates are a must.
A case in point
One product line that we supply, fire dampers, must be fire tested in order to obtain the MED certificate. We recently conducted the test, in a large furnace, in the presence of the surveyor whose company issues the certificate. The damper had to withstand temperatures of about 900 degrees for one hour, and meet all other test criteria. Well it did, so we are now waiting for the certificates to be issued.
That might seem like just a detail, perhaps – but in fact, without these certificates, we cannot deliver these items for installation on ships. In fact, not having the right certificates can be a real showstopper. A certificate is a piece of paper, but it’s not just a piece of paper: it’s also our ticket to new and continuing business.
Products and processes
Now, it’s not just certifications for our products that we need to keep up to date, but also those for our business processes. In some cases, the certification covers a lot of territory: the ISO certifies our company’s entire management system, for instance. It could cover such areas as our sales process, or procurement, or our engineering workflows. Then again, it could be more focussed: how do we catch errors in drawings and technical specifications, and prevent them from re-occurring?
Certification: the hidden payoff
I mentioned above that there’s a fourth reason for keeping certifications up to date. It’s not so obvious, perhaps, but it may in fact be the most important to the long-term health of the business.
On the regulatory front, we have deadlines for compliance, and they just have to be met. On the business front, not having the required certificates would mean not being able to sign new customers or continue with existing ones. But having to keep everything up to date means something else, too: that we have to keep examining our processes, and looking for ways to improve, for new efficiencies, even for entirely new processes. In a word, then, certification is one more thing that keeps us on our toes, in continual-improvement mode, and focused not on maintenance of the status quo but on innovation.
If you think about it, then, what we have is a classic case of necessity, in the form of regulatory and standards compliance, as the mother of invention and constant renewal. And that makes it worth all the effort.
Harry Smit | Senior QESH Engineer
Harry Smit has been a senior engineer at the Quality, Environment, Safety and Health department of Heinen & Hopman since 2008.