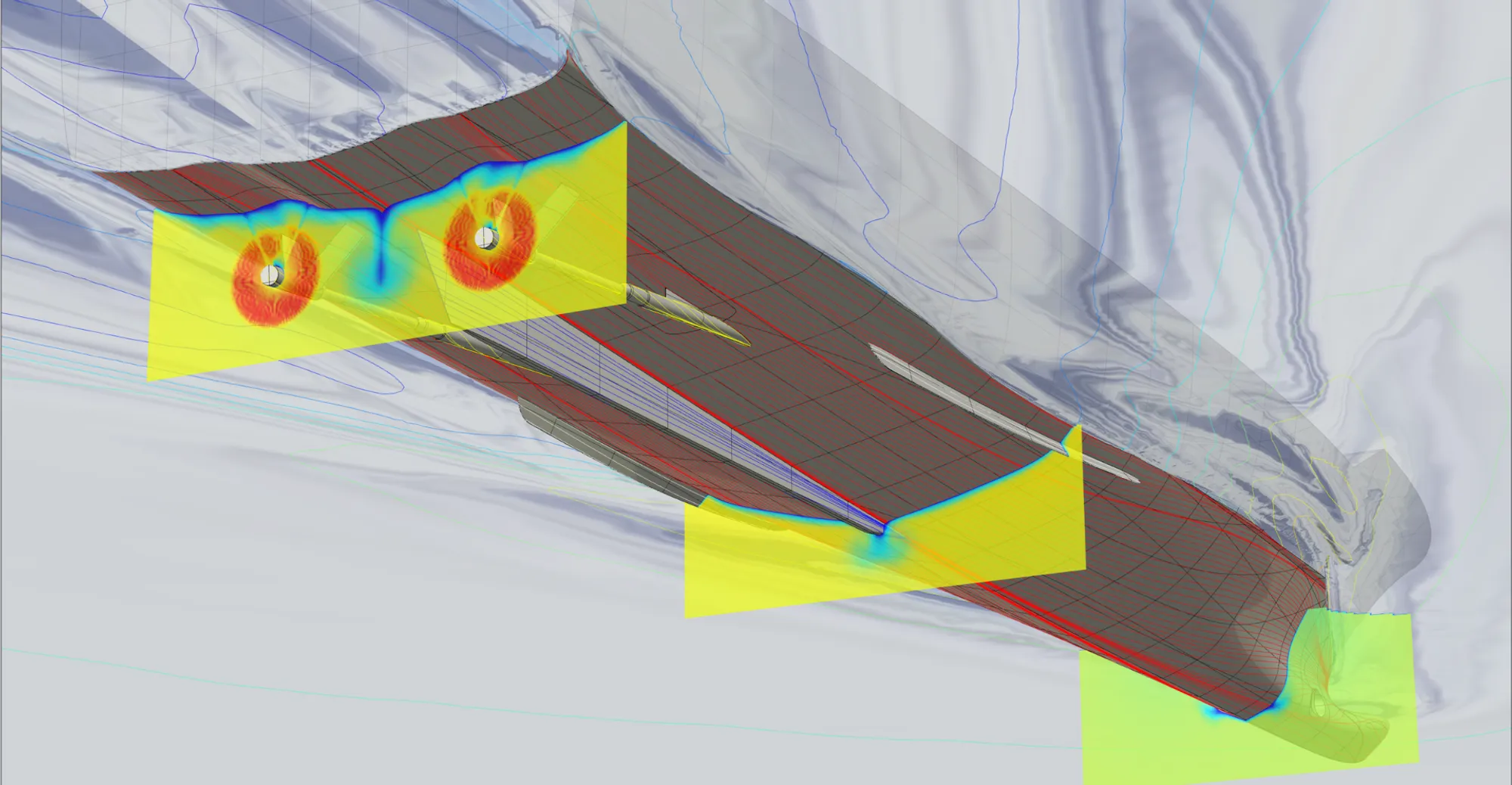
What is CFD? Computational Fluid Dynamics explained
– by Martijn Blok – 13/11/20
Computational Fluid Dynamics (CFD) creates a digital simulation that visualises the flow of fluids and the way they are affected by objects. It is a very powerful tool that shows in advance how temperature, pressure and velocity are going to behave in a design.
In this guide you’ll learn the following:
- How does CFD work?
- Why is CFD important?
- Is CFD hard?
- When to use CFD?
- How accurate is CFD?
Image 1: Gasoline evaporating from a gasoline spill.
1. How does CFD work?
Most of us are familiar with the breakdown strategy: chopping a big problem, task or activity into smaller and more manageable pieces. In a way this is how CFD works.
The problem with fluid dynamics is that it has many different properties such as heat, mass and velocity, all of which affect each other over the course of time. Encapsulating this in a mathematical model leads to the Navier-Stokes equations, a series of very complex partial differential equations involving more than one variable and their respective derivatives.
With CFD the area of fluid dynamics being analysed is represented as a closed system. This is an important factor as it sets the boundaries. In a closed system mass, momentum and energy are stable constants. Basically, everything must be conserved.
Next, this area is meshed – split up into multiple sub domains called cells. Each cell is linked with its nearby cells. Changing a variable in one cell has an impact on other cells. As is the case with a jigsaw puzzle, change one piece and many (or maybe all) pieces change with it. The puzzle is solved from the edges, from the boundary conditions, which define the in- and output of the fluid volume.
Image 2: Heat coming from engines
2. Why is CFD important?
Imagine you can peek into the future and see how your designed system is going to work before anything solid has been built. This gives you the ability to adjust and perfect your system even if you are still in the design phase.
A CFD model already gives you a good idea of how the system will operate in the design phase. It shows what will work and what not, allowing you to intervene at an early stage before anything has been constructed.
This is better for your state of mind and can also save a lot of money.
3. Is CFD hard?
The answer here depends entirely on the case at hand. Engine rooms are often a point of attention as every inch is used in these areas, leading to very complex models that need to be simplified in order to run a simulation.
The difficulty lies in deciding what may and may not be simplified, which details have an influence and which not. In addition, critical areas require more detail than others. Omitting the right elements can lead to an erroneous outcome.
Image 3: Meshed space around engine
4. When to use CFD?
CFD is used to find out how hotspots, air velocities and temperature levels work in a specific room. Although deployable in any space, it is usually applied in complex situations where you do not exactly know how certain properties will behave. An engine room, where hotspots and a lack of circulation can cause problems, are an obvious example.
For ordinary cabins or other spaces, a design based on knowledge and experience is fine. The calculations are relatively simple with problems rarely anticipated. But on superyachts and cruise vessels. where very high standards are demanded, CFD provides solid proof that you will meet the DNVGL comfort notation.
Image 4: Heat visualised
5. How accurate is CFD?
While the accuracy of the solution depends on several factors, the mesh structure is key. A CFD simulation is an approximation of reality: the coarser the mesh, the further you are from the actual situation. Dip below a certain accuracy level and the result is no longer realistic.
Areas in the model where the physical properties are critical require a finer mesh size. Failures can occur when the mesh does not cover all the effects that take place in one cell. The mesh contains multiple effects that will change as the mesh gets finer.
To obtain reliable results and ensure an accurate solution, analysts must take particular care with regards to the cell size, the number and position of cells and the computational time.
Conclusion
Computational Fluid Dynamics analyses and solves problems that involve flows like gases or liquids. Computers are used to simulate a model that shows how these fluids flow and interact with the surfaces and solids of the model. CFD is used to pre-engineer complex areas where the right temperature and flow are critical factors. The accuracy of the model depends on its detail.
Curious about how CFD can be used to solve your engineering challenges in advance and save you frustration, time and money? Contact one of our engineers and download the brochure for more information.
Martijn Blok | R&D Engineer
Martijn Blok has been working at Heinen & Hopman since 2013. During his study Integrated Product Development he learned to analyse and engineer the functional side of a new product. At Heinen & Hopman, Martijn is responsible for detail engineering using CFD-analysis amongst others to optimise our new products.