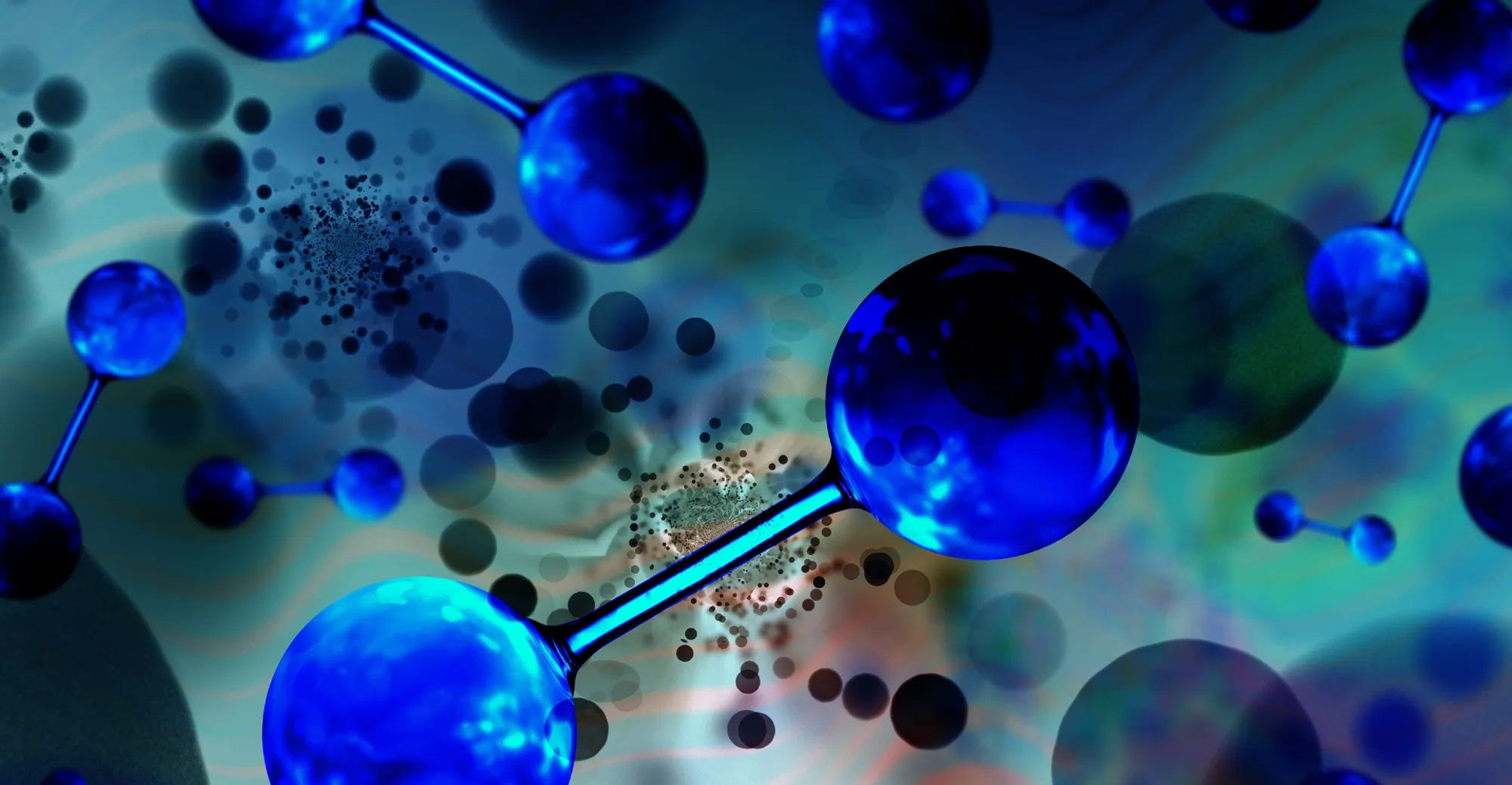
Sustainability: Refrigerants
Sustainability: Refrigerants
– by Sebastiaan Jansen, 13/04/21
A refrigerant loss in the range of 20 to 40% is reported annually in the maritime sector as ships are permanently buffeted by the continuous motion of wind and waves. The resulting damage and leaks causes refrigerant losses equivalent to 18.2 million tonnes of CO2, more than the annual emissions of a country like Croatia.
Full circle
The first cooling machines were introduced in the early 20th century and ran on refrigerants such as ammonia, CO2 and sulphur dioxide. Due to concerns about safety, toxicity, corrosion and high pressure, alternatives were sought that would cause less damage when leaks occurred.
American company Dupont was the first to come up with a refrigerant that did not have these negative properties, released under the brand name Freon R-12. These synthetic refrigerants were increasingly refined over the years, until we realised they were helping to destroy the ozone layer and fill our atmosphere with greenhouse gases. Now we’re returning to natural refrigerants which, ironically, are the ones replaced a century ago because they were considered toxic and dangerous.
The onboard situation
Today you see more and more onshore installations running on natural refrigerants, with the maritime sector lagging somewhat behind. Vessels launched before 2000 run on R-22 and the newer ones on R134a and R404a for air conditioning and provision cooling respectively. And not without reason… The disadvantages of natural refrigerants such as high pressure (CO2), toxicity (ammonia) and flammability (propane) can cause major difficulties with the leakage losses on ships and in the built-in technical rooms where cooling machines are located.
The perfect refrigerant
The perfect refrigerant does not affect the ozone layer and has a GWP of around 1 (GWP stands for Global Warming Potential and indicates the equivalent impact of CO2). But that’s not all: the refrigerant should ideally be non-corrosive, non-flammable and non-toxic.
Also, we have to consider the refrigerant’s boiling point, which must be just slightly below the desired cooling temperature. While you can of course play with this by changing the pressure, it’s best to avoid extremely high pressures – these are more dangerous and require stronger and more expensive materials.
The specific heat of the refrigerant must be taken into account too. That is the amount of energy it draws from the environment during evaporation.
The right direction
The search for the perfect refrigerant is a tough one, then, as there’s always something wrong. For example, a low GWP refrigerant such as R-1234ZE is registered as lower flammable (A2L) and cannot be used. In addition, ships have to deal with class bureaus that have yet to set regulations for these refrigerants so don’t accept them onboard.
Nonetheless, there’s a big difference between the GWP value of one synthetic refrigerant (R134a – GWP 1430) and the other (R515B – GWP 293). And although not perfect, these alternative refrigerants are a big step in the right direction and increasingly used.
Conclusion
Cooling installations on land are increasingly switching to natural refrigerants with a low GWP value. Cooling needs on ships are very different due to their continuous movement and more frequent leaks.
The downside of natural refrigerants is their toxicity and flammability, with agencies such as DNV and Lloyds each having their own rules for the use of highly flammable substances.
Despite this, progress is being made in the maritime sector. There are increasingly better synthetic refrigerants with only a fraction of the GWP value of commonly used refrigerants such as R134a and R404a.
Looking for a way to reduce your ecological footprint? Contact one of our engineers to see how a sustainable HVAC installation can contribute.
For everything HVAC stay tuned to heinenhopman.com.
Sebastiaan Jansen | Manager Cooling Department
Sebastiaan Jansen has been working at Heinen & Hopman since 1997. He started as assistant mechanic at our company and worked his way up to the position of Manager Cooling Department. Sebastiaan and his team are responsible for the engineering of the cooling systems for all kinds of Heinen & Hopman projects. He aims to achieve the highest quality systems through applying innovative technologies. A challenging, but interesting, task.