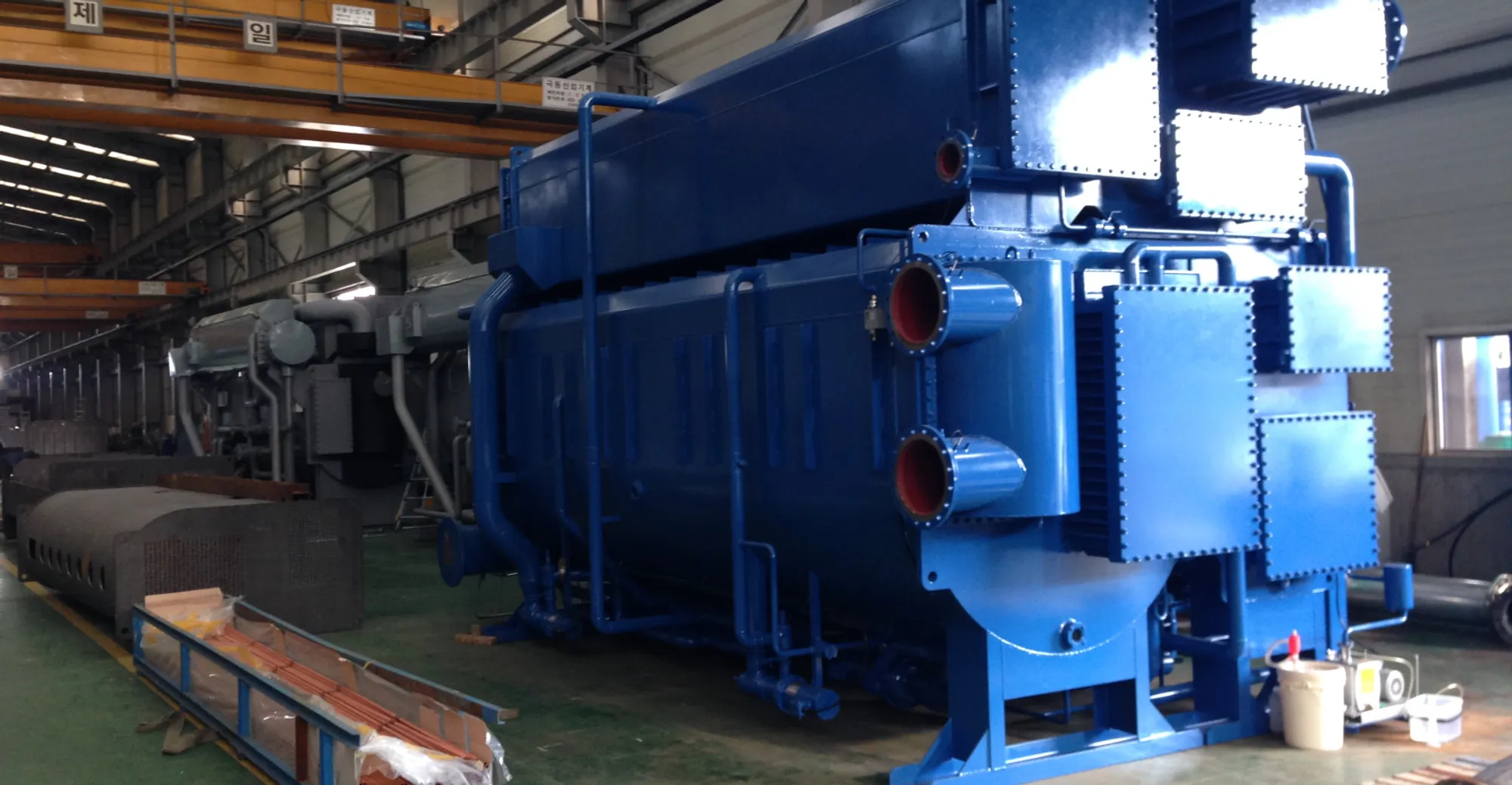
A user-friendly guide to absorption chillers
A user-friendly guide to absorption chillers
– by Sebastiaan Jansen, 09/10/20
Looking for a cooling machine that is highly energy efficient? A chiller that doesn’t make use of any environmentally harmful refrigerants or potentially global warming F-gases and that is low on service & maintenance costs? An absorption chiller may well be the answer…
In this guide we look at the basic principles of the absorption chiller and explore how it might be a solution for your project. We cover these three questions:
- What is an absorption chiller?
- How does an absorption chiller work?
- Where are absorption chillers used?
What is an absorption chiller?
An absorption chiller is a cooling machine that uses heat as its main source of power. Compared to a conventional chiller, the first thing that strikes you is the total absence of a compressor, the normal driving force (and power consumer) of a machine. Instead, absorption chillers use a heat source (waste heat) to fuel their physical processes, producing chilled water while consuming just a small amount of electricity to run the unit’s pumps.
Image of Absorption Chiller
Another significant difference with a conventional chiller is the absence of refrigerant. An absorption cooling machine runs on a mixture of water and lithium bromide. The latter is highly hygroscopic, which means it attracts and holds water molecules via absorption from the surrounding environment.
The only moving parts inside an absorption chiller are some circulation pumps, needed to circulate the different mediums.
How does an absorption chiller work?
An absorption chiller mainly comprises four chambers, all connected to each other. A different physical process takes place in each chamber of a simplified version such as our example here.
Image of four chambers
Generator
In this chamber the water vapour (H2O) is separated from the lithium bromide (LiBr). Waste heat at high temperatures (95/75°C), heats up the H2O/LiBr mixture and causes the H2O to evaporate. Water vapour floats to the condenser chamber while the remaining mixture flows back to the absorber.
Condenser
This chamber contains a heat exchanger with sea water or fresh water running through it. The water vapour starts to cool down and eventually condenses into a liquid. From here the liquid H2O flows into the evaporator.
Evaporator
This is where the actual cooling process takes place. The low partial pressure in this chamber causes the water to evaporate at a low temperature. This phenomenon extracts heat out of the environment, which is the chilled water heat exchanger running through the chamber.
Absorber
The almost pure mixture of lithium bromide pouring from the generator has an irresistible attraction to the water from the evaporator chamber. This hygroscopic effect pulls the H2O out of the chamber in its wake, lowering the pressure inside the evaporation chamber. The H2O/LiBr mixture is pumped to the generator chamber.
All the chambers in action
Where are absorption chillers used?
Absorption chillers are used wherever waste heat or low-cost thermal driving heat sources are available. As heat is the main power source it is a necessity when using an absorption chiller.
Waste heat source
Electric generators and propulsion engines generate a lot of (waste) heat, making them a good source to tap into… Presuming that they are operational. While this is constantly the case with offshore rigs and FPSOs, cruise and passenger ships have harbour time to take into account.
Nonetheless, the use of an absorption chiller can still be justified with such vessels as their heat load will be at a minimum in harbour mode. When combined with electric chillers an absorption chiller will neutralise the maximum heat load when the vessel is fully operational.
Absorption chiller in combination with electrical chillers
Final thoughts
The use of absorption chillers in the maritime sector brings an extra challenge. Stationed in the pump room of a ship, some negative effects can occur such as performance de-rating. This is due to the refrigerant overflowing and mixing caused by ship motions, pitching and rolling. H&H’s Maritime Absorption Chiller is therefore designed with special welding and structure strength to counter these effects.
Sebastiaan Jansen | Manager Cooling Department
Sebastiaan Jansen has been working at Heinen & Hopman since 1997. He started as assistant mechanic at our company and worked his way up to the position of Manager Cooling Department. Sebastiaan and his team are responsible for the engineering of the cooling systems for all kinds of Heinen & Hopman projects. He aims to achieve the highest quality systems through applying innovative technologies. A challenging, but interesting, task.